What Does A Gas Barrier Membrane Do And Why Is It Important?
- straight2site
- 3 days ago
- 7 min read
A Gas Barrier Membrane is essential when building on land that may release harmful underground gases. These gases—like Radon, methane, and carbon dioxide—can seep into buildings unnoticed. Without proper protection, they pose serious risks to health and safety. Installing a gas membrane helps create a safer environment for occupants and ensures compliance with UK construction and environmental regulations. These membranes are widely available through reputable building suppliers, making it easier to source the right materials for effective protection.

What Is a Gas Barrier Membrane?
A gas barrier membrane is a protective layer used in construction to block harmful ground gases from entering buildings. These gases may include radon, methane, and carbon dioxide, which can pose health risks to occupants if left uncontrolled. The membrane is typically installed beneath floor slabs or within the base of a building’s foundation. It creates a sealed barrier between the ground and the internal space above.
Most gas membranes are made from strong, flexible materials like reinforced plastic or multi-layered composites. These are designed to resist tears, chemical damage, and pressure from soil movement. The membrane must be joined and sealed properly to be fully effective. Even small gaps or poor overlaps can allow gas to seep through and compromise the protection.
Gas barrier membranes are critical on brownfield, industrial, or contaminated sites where ground gases are more likely to be present. By adding this layer early in the build, you reduce long-term risks and comply with UK construction standards. It’s a small investment with long-term safety benefits.
Why Is a Gas Membrane Required?
Gas membranes are required on sites where there is a risk from harmful ground gases or chemical vapours. These risks are identified through a professional ground gas assessment, usually done before construction begins. If the report finds permanent gas threats or volatile organic compounds (VOCs), a membrane becomes essential.
UK regulations require certain levels of gas protection based on the site’s risk level. This ensures buildings meet health and safety standards. Without proper protection, gas can enter through cracks, pipe routes, wall cavities, and construction joints. Even the smallest gap can let dangerous gas into the building.
Installing a gas membrane reduces the risk of exposure to harmful substances. It also protects the long-term health of building occupants. By following regulations early, developers avoid costly repairs and safety concerns later on. A compliant membrane system supports safe, legal, and reliable construction across a wide range of sites.
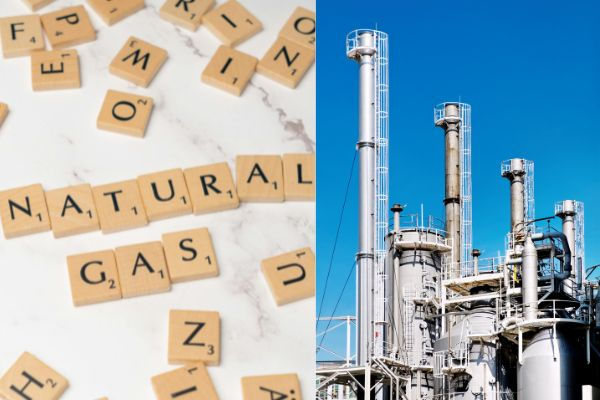
What Are the Types of Ground Gases?
Ground gases are often present beneath construction sites and can pose serious health and safety risks if left unmanaged. The most common ground gases are carbon dioxide and methane, both created when microorganisms break down organic material in the soil. These gases are commonly found near landfill sites, wetlands, areas with organic-rich soils, or ground affected by backfill.
Natural geological formations can also release harmful gases. These include coal seams, limestone beds, and rock layers containing uranium. While carbon dioxide and methane are widespread, several other gases can also pose significant risks:
Radon
A radioactive gas that we cannot see, smell or taste. It occurs naturally in areas with specific rock types.
Carbon Dioxide (CO₂)
A common gas near landfills, but it can also arise from natural soil processes.
It may build up to harmful levels without proper gas barriers.
Carbon Monoxide (CO)
Found in both natural and human-influenced environments.
It is toxic, odorous, flammable, and potentially explosive.
Methane (CH₄)
Frequently associated with former landfill or brownfield sites.
Gas protection should follow BS 8485:2015+A1:2019 standards.
Hydrogen Sulphide (H₂S)
Highly toxic and flammable, with a strong odour like rotten eggs.
It can irritate the eyes, nose and throat even at low levels.
Volatile Organic Compounds (VOCs)
These are gases emitted from certain solids or liquids, often from past industrial use.
Proper site assessment is required to manage VOC risks safely.
Identifying which gases are present is a crucial first step in any development. This ensures the right protective measures are installed and regulations are met.
How Does Ground Gas Become a Problem?
Ground gases can build up in both brownfield and greenfield sites. They may come from natural sources or past land use. This includes industrial activity, waste disposal, or the breakdown of organic materials underground.
When gases like methane or carbon dioxide accumulate, they can enter buildings through cracks or weak points. These include service ducts, construction joints, and even small gaps in floors or walls. If trapped indoors, they may create severe safety risks for occupants.
The dangers include:
Explosion risk – Methane is highly flammable and can ignite if allowed to build up.
Suffocation – High levels of carbon dioxide can displace oxygen in enclosed spaces.
Health impacts – Even low-level exposure over time can cause illness, headaches, or respiratory problems.
Structural damage – Pressure from trapped gas can weaken the foundation or damage floors and walls.
There have been multiple reported deaths linked to ground gas entering homes. While rare, these cases highlight how dangerous untreated gas ingress can be. That’s why early detection and prevention are critical on all development sites.
How Can I Protect Against Ground Gas?
Protecting against ground gas is essential in any new development. Everyone involved in construction must consider these risks early in the design phase. Ground gases can still enter buildings after completion if the correct protection is not installed.
The most common method of protection is using a ground gas barrier membrane. These membranes stop harmful gases from rising into buildings from the soil below. They are made from polymers, making them lightweight, flexible, and easy to shape during installation.
To ensure full protection, several measures can be combined. A ground gas specialist may recommend:
Gas barrier membranes – A continuous layer that blocks gas flow through floors and walls.
Ventilation layers – Help redirect gases safely away from the structure.
Sealing service entries – Prevent gas from entering through pipes or ducts.
Positive pressurisation or sub-floor systems – Used in more high-risk cases.
No matter the method used, the installation must meet high standards. UK best practice is outlined in CIRIA C735, which provides guidance on testing and verification. An independent gas protection specialist must also approve the system to confirm compliance and safety.
Early planning, the right materials, and professional oversight are key to protecting buildings from ground gas risks.

The Benefits of Gas Membranes
Gas membranes offer essential protection in modern construction, especially when developing sites affected by ground gas or excess moisture. These barriers are increasingly used in residential, commercial, and industrial projects. They provide several key benefits that support safer, more efficient, and longer-lasting buildings.
Key Advantages Include:
Radon Protection
Radon gas is a serious concern in many parts of the UK. It naturally escapes from certain rock types and can enter buildings unnoticed. Installing a gas membrane beneath the foundation helps block radon before it reaches indoor spaces. This significantly reduces health risks, especially the link between radon exposure and lung cancer.
Regulatory Compliance
UK building regulations require radon protection in specific regions, especially in new builds and extensions. Gas membranes help meet these legal obligations. Bodies like the National House-Building Council (NHBC) and the Property Care Association (PCA) support the use of membranes in high-risk areas.
Moisture Control
The UK’s damp climate increases the risk of moisture problems in buildings. Gas membranes also act as vapour barriers. They prevent water vapour from entering the building fabric, reducing mould, rot, and structural issues. This leads to healthier living conditions and longer-lasting materials.
Improved Energy Efficiency
Some advanced gas membranes also function as air barriers. They help reduce unwanted airflow and heat loss in winter. In summer, they limit heat gain. This improved insulation lowers energy use for heating and cooling, cutting both utility bills and carbon emissions.
Long-Term Durability
Gas membranes shield foundations and internal materials from long-term damage. By preventing gas and moisture ingress, they extend the life of the building’s structure. This lowers maintenance costs and helps protect property value over time.
Gas membranes are not just safety features—they're smart investments. They support compliance, comfort, and sustainability for years to come.
Conclusion: Why Gas Barrier Membranes Are a Smart Investment
Gas barrier membranes are vital for keeping buildings safe, compliant, and long-lasting.
They stop dangerous gases from entering indoor spaces through the ground or foundation.
These include radon, methane, carbon dioxide, and other harmful gases like VOCs and hydrogen sulphide.
Membranes also reduce moisture and damp, preventing mould, rot, and structural issues.
This dual function improves indoor air quality and helps maintain a building's integrity over time.
Correct installation also supports better energy efficiency and reduces long-term maintenance costs. In the UK, following standards like CIRIA C735 and BS 8485 ensures you're both legally compliant and safe. These guidelines help you select the correct gas membrane and install it properly. Gas membranes are not just a box-ticking exercise—they represent a strategic decision for long-term safety and value. Whether you're a builder, developer, or homeowner, sourcing high-quality products from trusted building materials suppliers adds an extra layer of protection and peace of mind. Early investment in the right system can prevent costly repairs and potential health risks down the line. A solid foundation begins with proper protection—choose a certified gas membrane system from day one.
FAQs: Common Questions About Gas Membranes
1. What is a gas barrier membrane?
A gas barrier membrane prevents harmful ground gases from entering buildings through floors or foundations.
2. Do I need a gas membrane for my project?
Yes—if your site has a gas risk, or it's located in a radon-affected area, a membrane is essential.
3. Which gases do gas membranes protect against?
They protect against radon, methane, carbon dioxide, VOCs, and hydrogen sulphide—depending on the system used.
4. Are gas membranes required by law in the UK?
Yes. In high-risk areas, they are required under Building Regulations and BS 8485 guidance.
5. Can gas membranes help with damp or moisture?
Yes. Many membranes also act as vapour barriers, reducing damp and preventing mould or building damage.
6. Who should install a gas membrane system?
Always use trained, certified professionals to ensure the membrane performs properly and meets UK standards.
Comentários