Does A Gas Barrier Membrane Offer Waterproof Protection?
- straight2site
- Apr 7
- 10 min read
As construction continues to expand into challenging environments, protecting buildings from below-ground risks has become more important than ever. One common question that arises during project planning is whether a gas barrier membrane can also provide effective waterproofing. While gas membranes are primarily designed to block harmful underground gases, many modern systems are now engineered to offer dual protection—shielding structures from both moisture and gas intrusion. This combined functionality not only simplifies the installation process but also helps reduce long-term risks linked to water damage and air quality concerns. Choosing the right type of membrane early in the design phase ensures greater structural integrity, regulatory compliance, and occupant safety. In this article, we explore how gas membranes work, their waterproofing potential, and what factors influence the best solution for different site conditions.
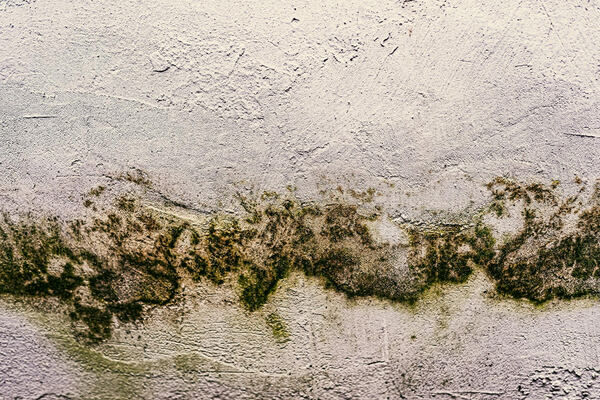
The Hidden Risks: Moisture and Gas Infiltration in Buildings
Persistent moisture ingress poses a significant threat to the long-term durability of concrete structures, including walls, foundations, and subfloors. Concrete is naturally porous, making it vulnerable to groundwater and chemical contaminants present in the soil. Over time, these substances can seep into cracks and voids, weakening the material, damaging surfaces, and corroding internal steel reinforcement. Prolonged exposure to moisture can also affect internal components, increasing the likelihood of condensation, damp-related damage, and potential health issues such as mould growth for occupants.
Alongside moisture concerns, there is growing awareness of the risks linked to gas intrusion—particularly methane and industrial solvents like trichloroethylene (TCE) and perchloroethylene (PCE). Methane, a hydrocarbon gas, not only contributes to climate change but also poses health and safety risks indoors. As a result, UK regulations and industry guidance continue to evolve, encouraging the use of membranes that offer protection from both water and harmful gases beneath new buildings.
Key Requirements for Effective Barrier Protection
Choosing the right membrane for structural protection means ensuring it meets several essential performance standards. The membrane should be:
Seamless, with no gaps where water or gas could get through
Securely bonded to the concrete surface, leaving no spaces that allow movement between the barrier and the base
Tough and long-lasting, able to handle environmental exposure for the full lifespan of the structure
Simple to install, working well with standard tools and typical installer experience
Reliable in practice, with proven results in real-world applications
Supported by a trusted provider known for both product development and technical support

Reliable Pre-applied Waterproofing Solution for Long-Lasting Protection
A durable, pre-applied waterproofing membrane combines a tough high-density polyethylene (HDPE) layer with a pressure-sensitive adhesive and a weather-resistant coating. It’s designed for direct application onto formwork or soil retention systems before placing steel reinforcement. Once concrete is poured, the membrane bonds securely to the surface, forming a strong, continuous seal.
This system requires no water activation, pressure, or chemical treatment to initiate the bond. After installation, the membrane is immediately trafficable, allowing reinforcement to be set in place without delay. It remains stable under typical site conditions, including moisture exposure and repeated freeze-thaw cycles, ensuring long-term reliability.
High-Performance Self-Adhesive Waterproofing Membrane
This self-adhesive, cold-applied membrane is designed for both above-ground and below-ground waterproofing. Suitable for horizontal and vertical surfaces, it provides reliable protection in a variety of construction settings. The membrane includes a durable HDPE composite carrier film, delivering enhanced strength and long-lasting performance. Backed by over five decades of proven results across diverse environments, this technology continues to support effective waterproofing on projects of all sizes.
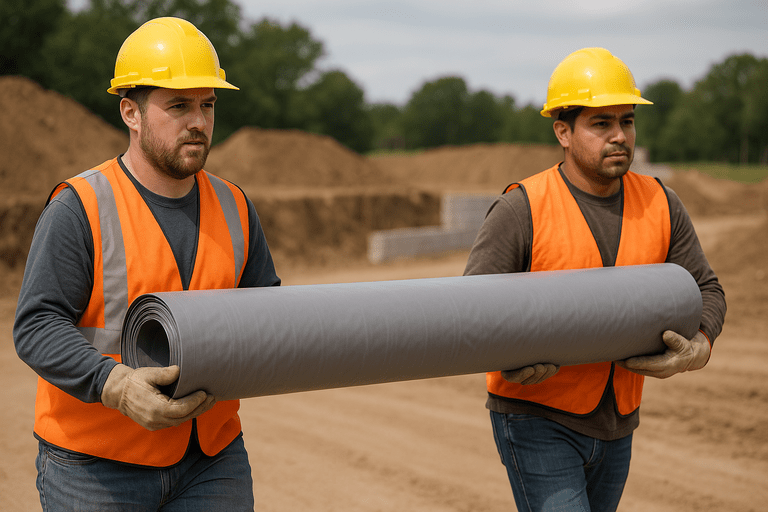
Why Choosing the Right Thickness of HDPE Membranes Matters for Long-Term Protection
The lasting performance of high-density polyethylene (HDPE) and HDPE composite membranes depends heavily on using the right material thickness. When applied correctly, these membranes provide a strong barrier against water and gas, thanks to the unique properties of HDPE as a thermoplastic polymer.
HDPE is known for being chemically stable and highly resistant to breakdown over time. In contrast, some other materials used in waterproofing membranes—like linear low-density polyethylene (LLDPE), polyvinyl chloride (PVC), ethylene propylene diene monomer (EPDM), and chlorosulphonated polyethylene (CSPE)—are more prone to deterioration. LLDPE, PVC, and EPDM often degrade through oxidation, while CSPE is vulnerable to dehydrochlorination. HDPE, however, stands out for its stronger resistance to oxidation, hydrolysis, and physical stress, making it a reliable option for long-term use as a geomembrane.
Independent lab tests have shown that HDPE maintains its performance better than many other membrane types, whether the material is exposed to the elements or remains covered.

Understanding Chemical Permeation Resistance in Waterproofing Membranes
Chlorinated solvents like tetrachloroethylene (PCE) and trichloroethylene (TCE) are commonly found in groundwater and surface water across various regions. This raises the chance that waterproofing membranes may come into contact with these and similar chemical pollutants. As a result, it’s important to understand how different membrane materials perform when exposed to such substances.
The resistance of high-density polyethylene (HDPE) membranes, such as those used in advanced waterproofing products, was assessed against volatile organic compounds. This was compared with membranes made from non-HDPE materials to gauge relative effectiveness.
In tests based on the ASTM F739 method, membranes were immersed in a mix of reagent-grade TCE and distilled water. An open-loop system was used, and gas chromatography helped track chemical permeation over time. Across all tested temperatures, the HDPE membranes showed significantly better resistance to chemical permeation than their non-HDPE counterparts.

Strong Bonding and Lateral Water Resistance Testing
Maintaining a continuous bond between a waterproofing membrane and the concrete surface is essential for long-term protection. A secure attachment stops water or gas from moving sideways between the structure and the membrane, which can otherwise lead to hidden leaks and structural damage over time.
Some advanced membranes use bonding technologies that create a direct seal with the concrete when poured. Unlike systems that rely on chemical or mechanical bonding, these membranes form a seamless, consistent connection that lasts for the life of the building.
When tested against industry standards, high-performing membranes have shown stronger bond strength and greater resistance to hydrostatic pressure compared to conventional options. In some cases, lateral water resistance was maintained at pressures over double that of other membranes.
Long-term testing has also confirmed these membranes retain their effectiveness under real-world conditions. Over multi-year trials, even with sections deliberately left exposed, they continued to prevent lateral water migration, proving their value for durable below-ground protection.
Durable Concrete Bonding That Lasts in Harsh Conditions
Post-applied waterproofing membranes that use pressure-sensitive adhesive (PSA) technology create a strong bond when applied to properly prepared concrete surfaces. These advanced adhesives have been tested to withstand pressures exceeding 700 KPa—equivalent to roughly 70 metres of water head or 99 psi.
This level of bonding strength ensures a secure, long-lasting seal between the membrane and the structural concrete. Even in environments where constant water pressure is present, high-performance membranes with reliable adhesion properties can help prevent water ingress and maintain the integrity of the structure over time. Proper installation and surface preparation remain essential to achieving these results.
Gas-Resistant
Keeping harmful gases like methane, carbon dioxide, and radon out of buildings is crucial for meeting safety regulations and protecting the health of those inside. High-quality gas-resistant membranes play a key role in achieving this. Products that use HDPE or HDPE composite layers are particularly effective as these materials do not react with gases or chemicals. This makes them a reliable choice for forming a barrier against gas intrusion.
Independent testing has shown that some advanced membranes go beyond standard expectations. One such membrane has been certified to exceed the protection levels set out in BRE Reports 211 and 212, which relate to radon, methane, and carbon dioxide resistance.
In trials conducted at the University of London, another membrane demonstrated exceptional performance, with a methane permeability rate of just 3.89 millilitres per square metre per day. This is well below the British guidance limit of 360 millilitres, showing just how effective modern membranes can be in managing gas ingress.
Simplifying Waterproof Membrane Installation for Long-Term Reliability
Post-applied waterproofing membranes that use pressure-sensitive adhesive (PSA) technology form a strong, lasting bond when applied to well-prepared concrete surfaces. These advanced adhesives have demonstrated the ability to handle high levels of pressure—over 700 KPa, which equals around 70 metres of water head or 99 psi.
This strength ensures the membrane stays securely attached to the concrete, even under continuous water pressure. In demanding environments, a high-performance membrane with proven adhesion helps prevent water from penetrating the structure. To achieve the best results, it’s essential to follow proper installation practices and ensure the surface is clean and ready.
Trusted Solutions Backed by Decades of Expertise
For over five decades, industry-leading innovations in waterproofing have helped protect buildings and infrastructure in a wide range of conditions. These below-ground systems are trusted on both residential and commercial projects, including those built on complex or high-risk sites. What makes these solutions stand out is the extensive research, real-world testing, and focus on long-term performance. Many developments in this field have gone on to shape wider industry standards. With strong technical expertise and ongoing global support, construction teams can count on practical, expert guidance. On-site specialists are also available to support successful results at every stage of the build.

Comparing Gas Membranes with Traditional Waterproofing Materials
Not all protective membranes are created equal. Traditional waterproofing materials are mainly developed to prevent moisture from entering a structure, while gas membranes are designed to block underground gases. However, recent advancements have led to the development of systems that combine both functions. These dual-purpose membranes offer protection from water ingress and harmful gas intrusion in one product. Unlike conventional materials, combined membranes are often made from more resilient layers, providing longer-lasting protection against environmental challenges.
They also help streamline construction by reducing the need for multiple installations, which can lower material costs and labor time. For building projects where ground conditions pose multiple risks, using a multi-functional membrane improves overall reliability and performance. This approach also simplifies site planning, as one system can be chosen to meet both waterproofing and gas resistance needs. It's an efficient way to future-proof structures from below-ground threats that may otherwise cause long-term damage.
When to Use a Combined Gas and Waterproofing Membrane System
In building projects where the land carries multiple environmental risks, a single membrane that protects against both moisture and gas is often the most practical solution. These systems are particularly helpful in areas with limited ground quality or where underground contaminants may be present. Instead of layering separate membranes, which can create weak points if not applied correctly, a combined membrane simplifies installation and reduces the risk of failure.
Fewer layers mean fewer joints, which leads to better long-term sealing and less chance of leaks. These membranes are suitable for a wide range of structures, including homes, offices, or mixed-use developments. Whether you're dealing with groundwater, chemical vapours, or soil gases, using a product that tackles both hazards from the outset saves time and offers peace of mind. It's a straightforward way to meet performance expectations and protect buildings from potential underground damage that may go unseen for years.
Why Ground Conditions Should Guide Membrane Selection
No two building sites are the same, and ground conditions can vary greatly—even across short distances. Before choosing a protective membrane, it’s important to assess the land beneath the proposed structure. Soil type, moisture content, and possible underground gases all play a role in how effective a membrane will be once installed. For example, sites with high groundwater levels may require more robust waterproofing, while areas with unknown past usage could hold chemical residues or gas risks.
Selecting a membrane that addresses all potential threats helps reduce the need for future repairs or replacements. A thoughtful choice ensures the building remains protected, even under pressure from environmental changes over time. Conducting a thorough ground assessment early on not only informs the type of membrane needed but also supports better planning and compliance across the project. In short, knowing your ground conditions leads to better decisions and longer-lasting structural integrity.
Understanding Why Performance Standards Matter for Membranes
Performance expectations for building materials continue to rise, and protective membranes are no exception. Whether used for waterproofing, gas resistance, or both, these systems need to perform consistently under real-world conditions. That’s why membranes are often tested to meet specific durability, strength, and permeability benchmarks. These standards help ensure that materials remain effective long after installation, even in demanding environments.
For developers and contractors, choosing a membrane that aligns with recognised performance criteria reduces risks during and after construction. It also helps projects avoid delays due to inspection failures or regulatory issues. More importantly, selecting a membrane that meets proven benchmarks increases the likelihood of a structure remaining safe, dry, and free from harmful gas intrusion. Following standardised guidance makes it easier to compare products and choose one that suits both the site conditions and the long-term goals of the build. In short, strong performance standards equal stronger protection.
Final Thoughts
Selecting a membrane that offers both gas resistance and waterproofing is essential for protecting buildings from below-ground risks. As more projects move on to challenging plots, the threat of moisture ingress and harmful gas intrusion continues to rise. A high-quality barrier system acts as a reliable line of defense, improving long-term structural durability and helping meet modern environmental and safety standards. Whether you're developing residential, commercial, or mixed-use buildings, using a proven membrane solution from the start helps avoid future complications, delays, and costly repairs. With the right installation and materials, teams can safeguard foundations, support compliance, and protect occupant well-being. In today’s construction environment, strong below-ground protection is not just recommended, it’s a practical, forward-thinking investment that supports sustainable and secure building outcomes.
FAQs
Can a gas membrane block water, too?
Yes. Many gas membranes are engineered to resist both gas and water. These dual-purpose systems protect structures from moisture and harmful vapors, offering a reliable solution for below-ground applications. Always confirm the membrane’s specifications to ensure it provides full waterproofing as well as gas resistance.
What sets a gas membrane apart from a waterproof membrane?
A gas membrane blocks harmful vapours like methane or radon, while a waterproof membrane stops moisture from entering the structure. Some modern products combine both features, offering comprehensive protection in one layer. This combination can reduce installation time and improve long-term performance on challenging construction sites.
When should I use a combined gas and waterproofing membrane?
Use a dual-purpose membrane on contaminated or high-risk sites, such as brownfield land or areas with rising groundwater. These sites require strong barriers against both water and gases. A combined membrane ensures long-term protection, helps meet environmental regulations, and avoids future structural or health-related issues.
Do all gas membranes provide waterproof protection?
No. Not all gas membranes are waterproof. Some only resist vapour intrusion without moisture protection. To avoid issues, always select membranes that have been tested and certified for both water and gas resistance. This ensures complete protection and reduces the risk of future foundation damage.
How do I know if my project needs this type of membrane?
Evaluate the site’s risk level. If there's contamination, groundwater pressure, or gas presence, you’ll need a barrier that handles both threats. Using a certified dual-function membrane improves safety, supports compliance, and protects your investment from moisture damage and hazardous vapor intrusion over time.
Comments